HIV National Reference Laboratory, Bahamas
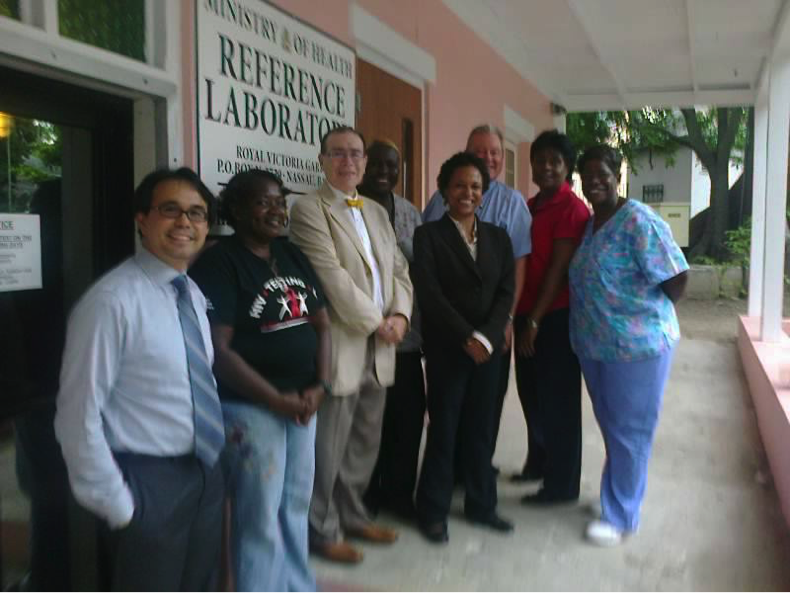
From left : Dr Ronald Chiu (CAP Assessor), Ms Vianna Williams (Ref Lab Phlebotomist), Dr Carlos Machicao (Lead CAP Assessor), Mrs Clarice Bain-Adderley (Ref Lab Security Officer), Dr Indira Martin (Lab Strengthening Manager), Dr Stan Read (Lab Director), Ms Marva Jervis (HIV Centre Managing Director), Ms Rochelle Sands (Ref Lab Medical Technologist).
Staff not in the photo : Mr Keith McConnell (Research Officer), Mr Desmond Ferguson (Phlebotomist), Ms Carisse Seymour (Cleaner)
- What was the hardest thing to do in order to get accredited?
Getting started. Most of us have worked in labs for many years without getting in-depth training in QMS. Fortunately, we were able to take advantage of the SLMTA training and mentorship program, which was funded by the PEPFAR/CDC agreement with technical partners AFENET. The training and mentorship was invaluable in terms of preparing us for accreditation and gave us the confidence and skills to begin the first steps of a long journey.
- What was the easiest?
The easiest was getting staff’s buy-in to the idea of aiming for quality and excellence.
- What was the most important contributing factor to getting accredited?
In one word, teamwork. It was extremely important to have all staff understand the accreditation process and its importance, and that all staff participated in the process and were motivated by it. We also had a great deal of support and encouragement from Ministry officials, which was truly indispensable. The SLMTA mentors were also absolutely pivotal to providing and conveying experience and know-how to both management and staff.
- What steps did you take?
SLMTA training was a critical first step, and the follow-up mentorship even more so. We started with the fundamentals- the Quality and Safety manuals and core technical SOPs and just branched out from there. We had to build systems, which was key, and systems building required communication and constant implementation. Staff meetings and meetings with the upper Ministry officials played a big role in communicating and standardising procedures in the lab, as well as creating an enabling environment for accreditation.
- What were the biggest mistakes you made?
The biggest mistake one can make on the road to accreditation is to consider any 'mishap', event or transgression as a 'mistake'; in the philosophy of effective Quality Management, there is no such thing as a mistake, only an opportunity for improvement. An effective QMS relies on flexibility and is dynamic and responsive to the prevailing conditions, and is also self-reflective and has the inherent ability to correct itself when in error (and this includes both technical and administrative matters). Therefore I can't say we made any 'mistakes' because without those events we could not have grown and continue to grow.
- What is the best advice you can give to others?
Accreditation is worth the work; it raises the overall quality of lab output in a way that is measurable and meaningful. It is a lot of work and the most important motivating force for your team is the quest for excellence. It is important to have a spirit of positivity and teamwork rather than one of reprimand, because this encourages honest constructive critique and self-correction. Accreditation is a process that requires participation of every member, from the cleaner to the lab director; everyone must know the value of their contribution.