Nyangabgwe Referral Hospital Laboratory, Botswana
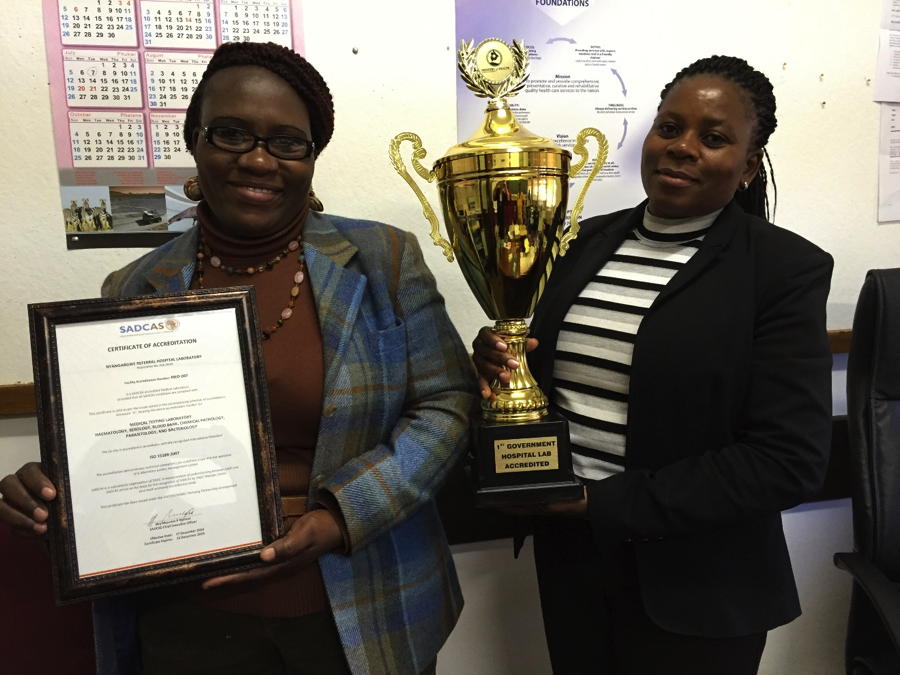
Left: Bazibi Moiteelasilo (Deputy Laboratory Manager) holding the SADCAS certificate of accreditation.
Right: Kelly Mokobela (Chief Medical Laboratory Scientist and Laboratory Manager) holding the trophy given by the government of Botswana for being the first government hospital laboratory ever accredited
- What was the hardest thing to do in order to get accredited?
Convincing the hospital staff to comply with our procedures according to SOPs. To overcome this challenge, we trained them on specimen handling and management requirements; the annual laboratory-clinician meeting also helped. The initiative to get the hospital accredited by the Council for Health Service Accreditation of Southern Africa (COHSASA) also helped change their mindset.
- What was the biggest success factor?
- Staffing the Quality Assurance positions (including QA officer, deputy QA officer, and biosafety officer) with the right people (those who are enthusiastic and motivated). Once we put the right people in those positions, things began moving. 2013 became a turning point for us.
- We involved everyone from the beginning.
- We had a supportive hospital superintendent. Accreditation is not cheap. He provided necessary resources for training and improvement work and critical advocacy to the clinicians.
- What was the most important contributing factor to getting accredited?
- Step 1 : Botswana Bureau of Standards (BOBS) trained key people on quality such as ISO15189 and documentation.
- Step 2 : We formed multiple committees so everyone was involved and had a specific role to play (e.g., quality, biosafety, equipment, supplies, housekeeping, scientific training, and even social).
- Step 3 : We developed SOPs - technical SOPs were developed before quality manual was written. All staff members were involved in reviewing the draft of system SOPs and providing feedback.
- Step 4 : We trained staff on SOPs developed and began implementing the system according to the SOPs.
- Step 5 : We monitored the implementation through internal audit, management review of logs, and laboratory indicators
- What is the best advice you can give to others?
- Start with the easier tasks – write technical SOPs before tackling the quality manual.
- Involve all staff members from the beginning.
- What were the benefits of getting accredited?
- Relationship with clinicians has improved significantly; evidence of this is in their compliance with specimen collection and management requirements
- Everyone is more vigilant of what they do. Chances of getting wrong results have decreased. Laboratory staff don’t just run QC. They also review the QC results and take corrective action before releasing the results (versus rushing to release results previously).
- During staff meeting, people are more inclined to suggest areas for improvement.
- Accreditation raised motivation. Staff are proud. They want to maintain it. It made them work harder.