Princess Marina Hospital Laboratory, Botswana
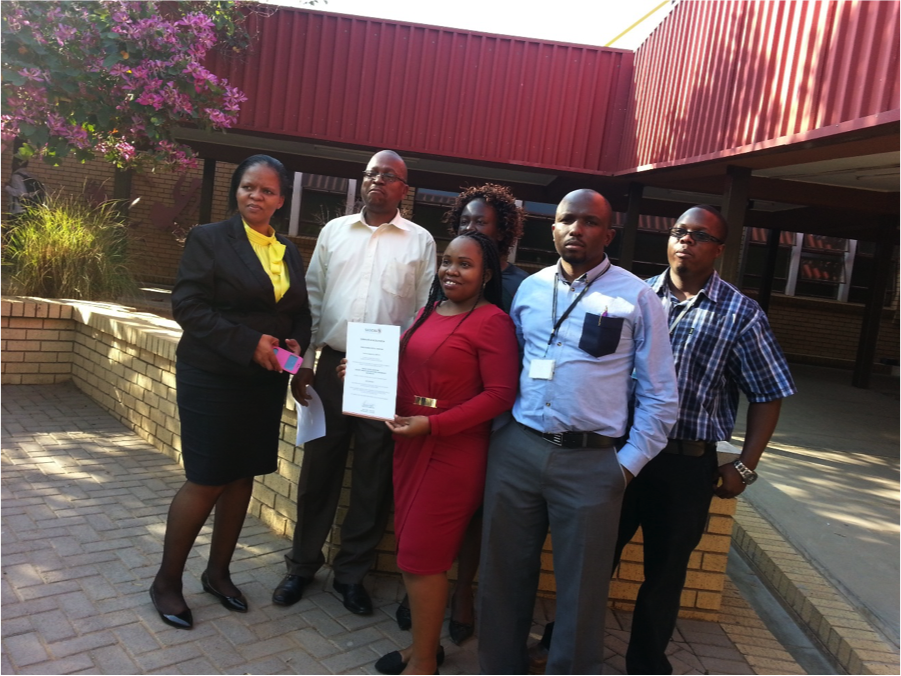
Back row from left: S. Johane (Quality Officer), T. Senosi (Laboratory Manager), L. Mudzikati (Head of Haematology), L. Masvingise (Deputy Quality Officer and Safety Officer)
Front row from left: B. Ngwako (Deputy Head of Chemistry), O. Chishawa (Head of Blood Bank)
- What was the hardest thing to do in order to get accredited?
- Quality Improvement Project in terms of time to complete them and understanding of the projects. We felt training should have been done onsite to cover all staff instead of selecting 2 people to attend SLMTA training at the Botswana Bureau of Standards.
- Management commitment – in terms of availing resources.
- Buy-in from clients – clinicians wanted their samples tested and had no concern for quality or safety. They wanted to come in holding samples in their hands and it was a challenge to make them understand the lab safety and quality requirements.
- Time and resources required to close non-conformities.
- What was the easiest?
Nothing was easy but communication within the lab – we understood each other.
- What was the most important contributing factor to getting accredited?
Staff commitment – they were always available and willing to put in extra hours.
- What steps did you take?
- Strengthened the quality office – a Senior Officer was assigned to the quality office.
- Started working on technical SOPs at the section level.
- Began implementing the management procedures. Implementation was reviewed daily in a one-hour morning meeting.
- What were the biggest mistakes you made?
Having too many consultants- they kept on cancelling/condemning each other’s work, especially those who prescribed ‘this is how you should do it’ without checking for staff understanding.
- What is the best advice you can give to others?
- Always have a plan – it is the sure way to succeed.
- Involve everyone from the beginning.